Highlights of the Study
Examples of ballistically tested multilayer plates
in collaboration with with Dr. S. Sedov at Ivan Chernyakhovsky National University of Defense (Ukraine)
No.6 Ti-6Al-4V/Ti-6Al-4V+10TiC
No.7 Ti-6Al-4V/Ti-6Al-4V+10TiC
No.12 Ti-6Al-4V/Ti-6Al-4V+ 5TiC/Ti-6Al-4V+10TiC
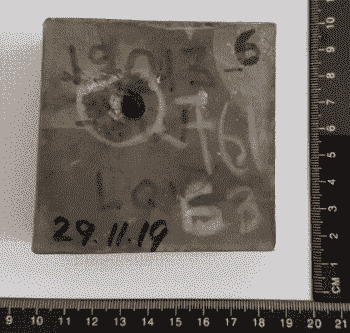
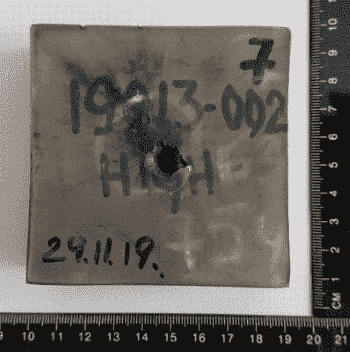
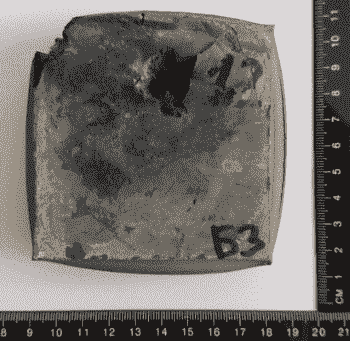
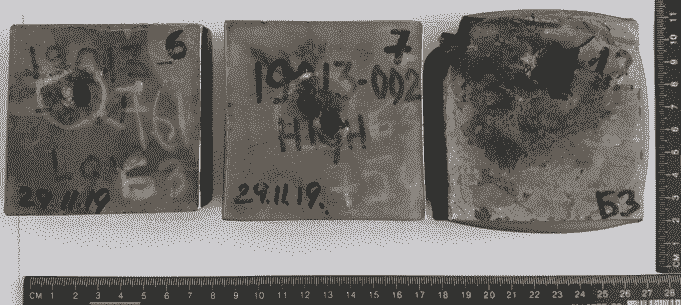
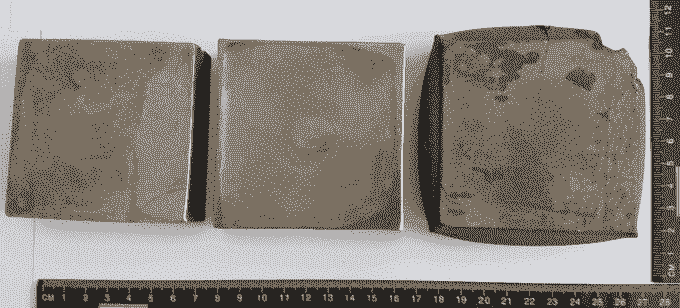
Results of Ballistic Test: Cast Ti-64 Alloy vs. BEPM Fabricated Layered Structures
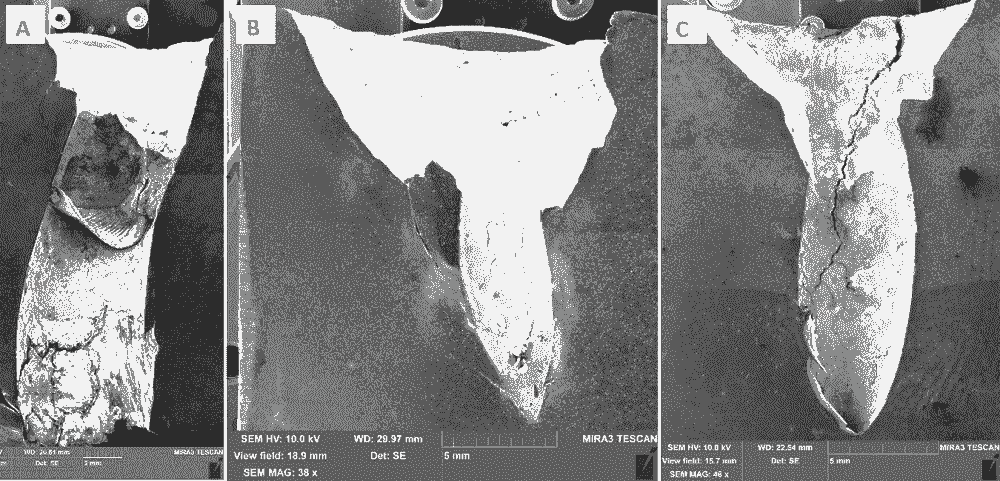
Figure 1: Ballistic test results A cast Ti-64 alloy; B bi-layered plate of Ti-64 // Ti-64 + 10% TiB; C three-layered plate of Ti-64 // Ti-64 + 10% TiC // Ti-64 + 5%TiC. All plates have about the same thickness 25-27 mm. Test conditions: B-32 bullet (caliber 7.62×54 mm, mass 10.4 g) kinetic energy 3500-3800 J. (In collaboration with Ivan Chernyakhovsky National University of Defense in Ukraine).
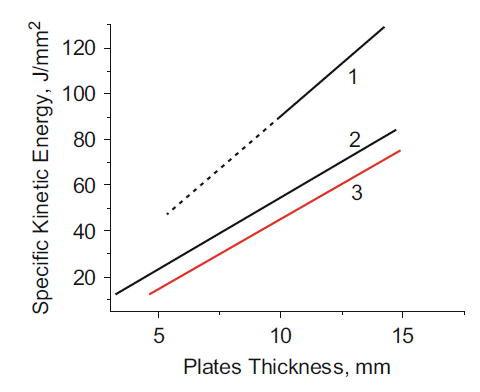
Figure 2: Specific Kinetic Energy of the 1st class (“soft” core) bullet required to make the armor piercing vs. plate thickness. Our current results using BEPM fabrication of Ti-64 alloy [1]. Previously reported studies on Ti-64 alloy cast & wrought + rapid surface heat treatment [2]; uniform alloy [3].
[1] S.V. Prikhodko, et.al., Titanium Armor with Gradient Structure: Advanced Technology for Fabrication, Advanced Technologies for Security Applications: Proceedings of the NATO Science for Peace and Security Cluster Workshop on Advanced Technologies, 17-18 September 2019, Leuven, Belgium, Springer, Ed. Claudio Palestini (2020) 127-143.
[2] O.M. Ivasishin, et.al, Progress in Physics of Metalls, 19(3) (2018) 309-334.
[3] J.C. Fanning, Journal of Materials Engineering and Performance, 14 (2005) 686-690.
Titanium Alloys vs. other Structural Armor Materials
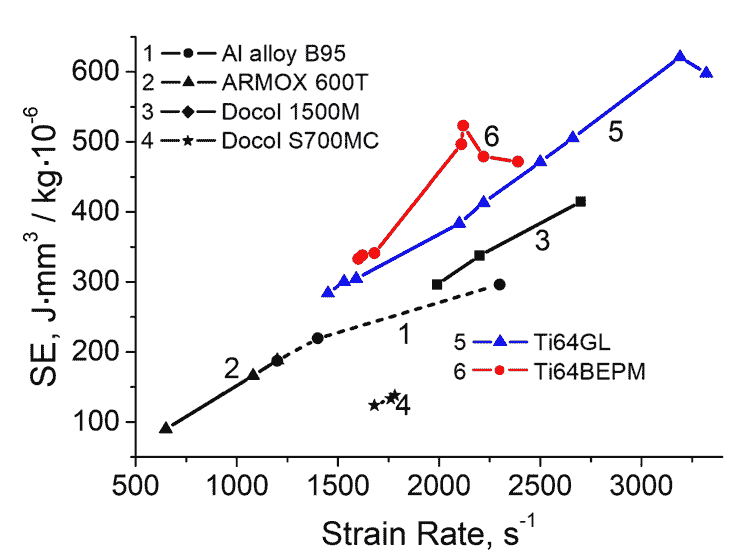
Figure 1: Strain Energy vs. Specific Strain Rate on high-rate Split Hopkinson Pressure Bar testing
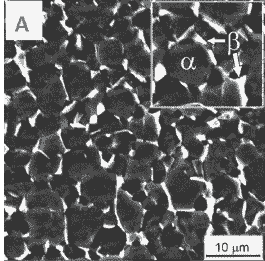
Figure 2: Alloy Ti-6Al-4V: A with globular microstructure (cast);
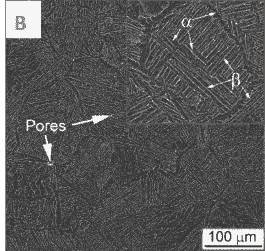
Figure 3: Alloy Ti-6Al-4V: B lamellar BEPM fabricated.
P.E. Markovsky, J. Janiszewski, V.I. Bondarchuk, O.O. Stasyuk, D.G. Savvakin, M.A. Skoryk, K. Cieplak, P. Dziewit, S.V. Prikhodko, Effect of Strain Rate on Microstructure Evolution and Mechanical Behavior of Titanium Based Materials, Metals (2020) DOI: 10.3390/met10111404
Superiority of Layered Ti/Composite Structures over Conventional Ti -Alloys
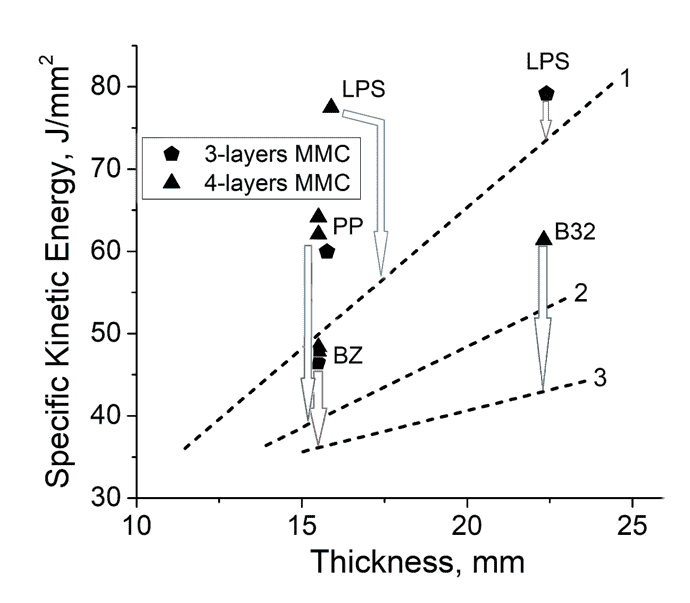
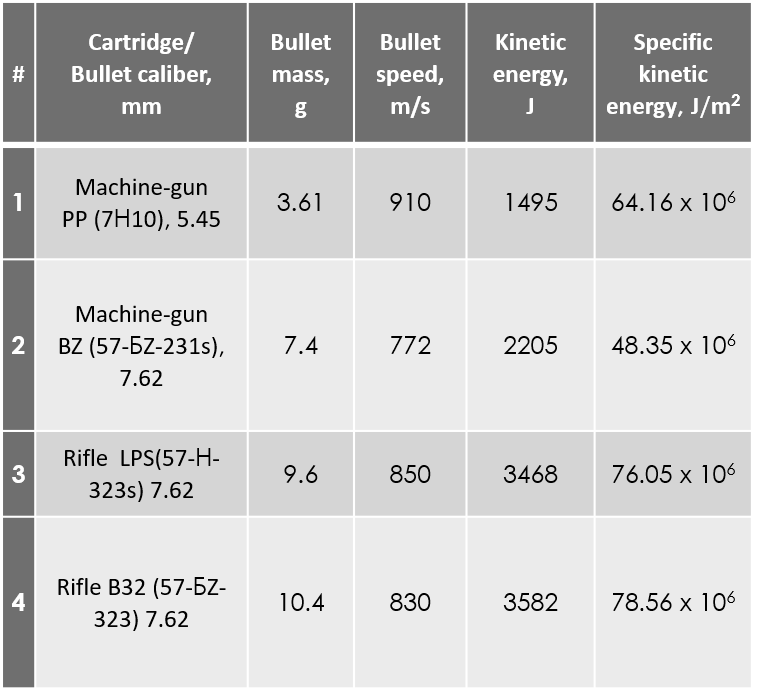
Figure 1: Efficiency of the bullet’s energy dissipation: A 3 striking factors: kinetic impact; hardened steel core; incendiary mixture; B 2 factors: kinetic impact; hardened steel core; C 1 factor: kinetic impact.
P.E. Markovsky, D.G. Savvakin, S.V. Prikhodko, O.O. Stasyuk, S.H. Sedov, V.A. Golub, V.A. Kurban, E.V. Stecenko, Microstructure and Ballistic Performance of Layered Armor Based on Ti-6Al-4V Alloy and Metal-Matrix Composites on Its Base Strengthened with TiC, Metallofizika (2020) 42 (11) 1509–1524. https://doi.org/10.15407/mfint.42.11.1509
High-Rate Strain Test with Split Hopkinson Pressure Bar
in collaboration with Prof. J. Janiszewski, from Military Technical University, Warsaw, Poland
Ti-6Al-4V
Ti-6Al-4V+TiC
Initial Machine Learning Model Development for Property Prediction and Alloy Design
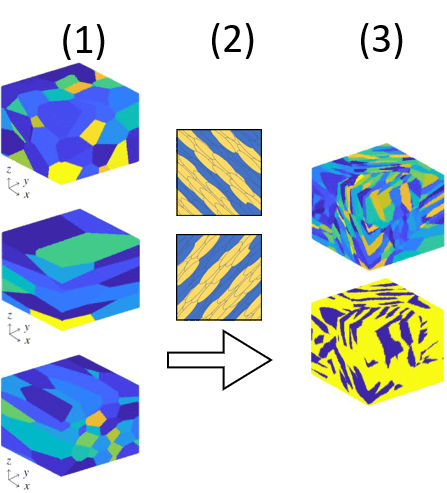
Figure 1: Schematic of formation process for finite element analysis of Ti-6Al-4V cubic volumes. Grains formed in (1) are “filled” with lamellae in (2). Final structure shown in (3). Upper image shows orientation, lower shows phase.
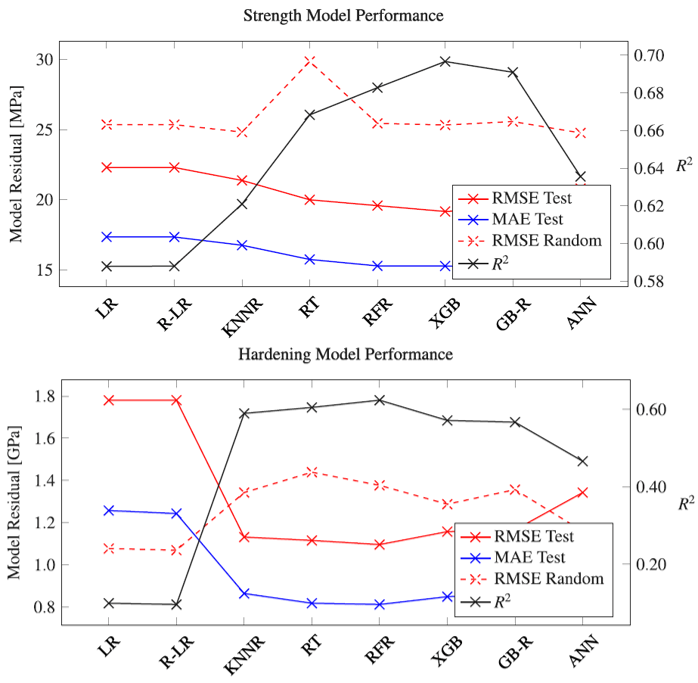
Figure 2: Machine learning model performance based on training from (A) yield strength and (B) post-yield hardening data obtained from computationally modeled samples.
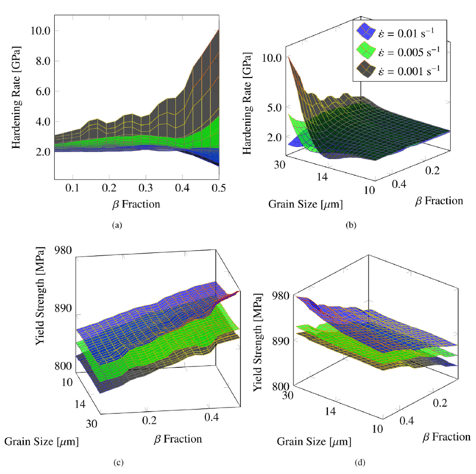
Figure 3: Predictions of (A)-(B)hardening rate and (C)-(D)yield strength as a function of grain size and β fraction for weighted voting regressor. Each plot contains three planes plotted in black, green, and blue that correspond to 𝜖̇ values of 0.001, 0.005, and 0.01 s−1, respectively.
Deformation Mechanism and Structural Changes in the Globular
Ti-6Al-4V Alloy under Quasi-Static and Dynamic Compression
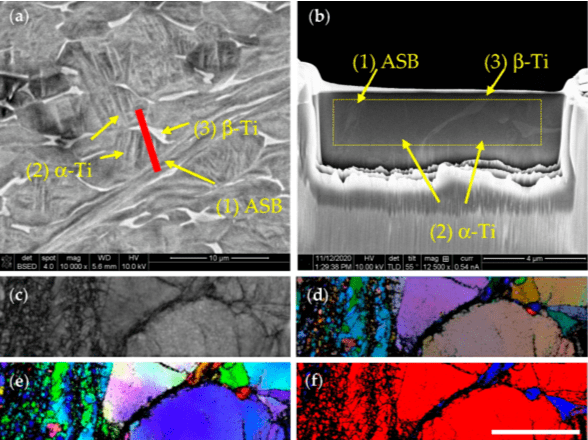
Figure 1: FSEM images (A,B) of the area in vicinity of the Adiabatic Shear Band (ASB) (highly deformed area of material) where the lift-off sample was cut and (C-F) Transmission Kikuchi Diffraction (TKD) framework data. The sample cut (shown with red section) crosses : a few α- and β-Ti grains and the ASB area labeled in (A,B). The image of the lift-off region (B) and the TKD analyzed area highlighted with yellow-dashed rectangular. Quality map (C); grains map in random color (D); orientation map (E) phase map showing α-Ti in red and β-Ti in blue (F). The scale bar in (F) is 2.5 μm.
P.E. Markovsky, J. Janiszewski, O. Dekhtyar, M. Mecklenburg, S.V. Prikhodko. Deformation Mechanism and Structural Changes in the Globular Ti-6Al-4V Alloy under Quasi-Static and Dynamic Compression: To the Question of the Controlling Phase in the Deformation of α+β Titanium Alloys. Crystals (2022), 12, 645. DOI: https://doi.org/10.3390/cryst12050645
Titanium Based Composites with TiC or TiB under Quasi-Static and High Strain-Rate Compression
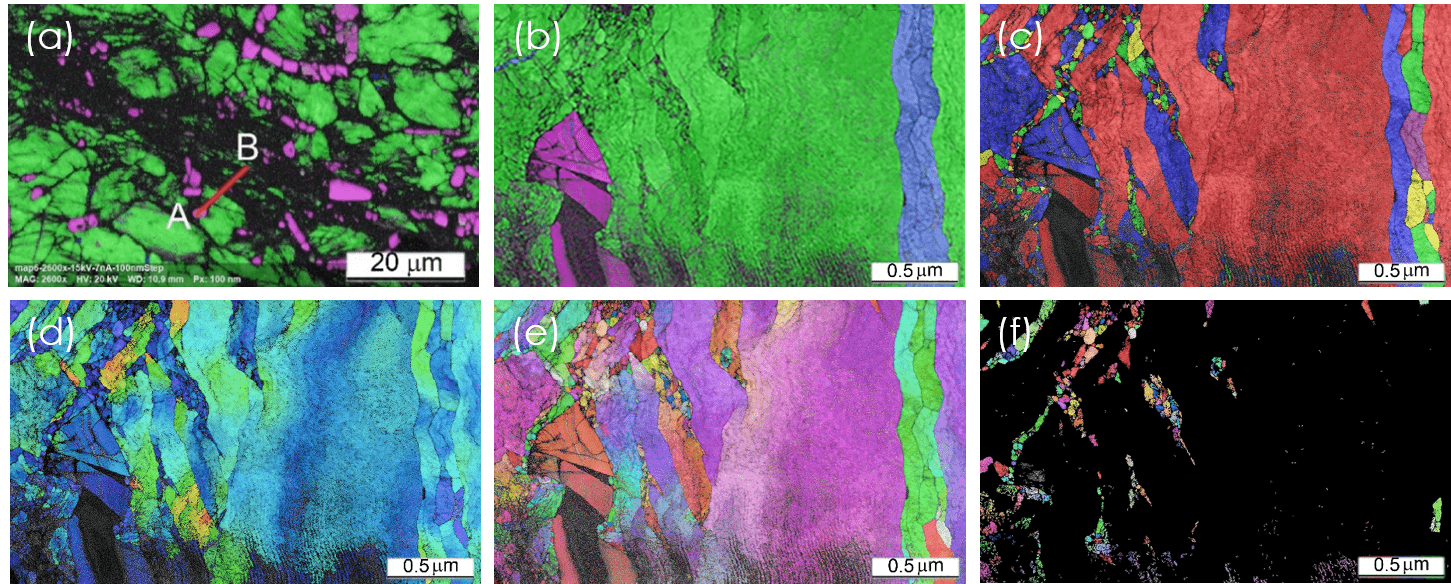
Figure 1: Conventional EBSD phase map (A) and TKD results (B-F) of the heavily deformed region of the Adiabatic Shear Band (ASB) of the sample Ti64 + 10TiB after dynamic HSRC test with the strain rate 2510 s−1. EBSD phase map in (A) showing the area where the lift-off sample (AB section in (A)) for TKD was taken; within α-phase is shown in green, β-phase in blue and TiB is in magenta colors. TKD results: phase map (B), similarly color coded as in (A); grains map, in random color (C); Grain Average Misorientation map (D); Inverse Pole Figure in z axis (E); IPFz map showing all grains <100 nm as a result of recrystallization (F).
P.E. Markovsky, J. Janiszewski; O.O. Stasyuk, V.I. Bondarchuk, D.G. Savvakin, K.Cieplak, D. Goran, P. Soni, S.V. Prikhodko, Mechanical Behavior of Titanium Based Metal Matrix Composites Reinforced with TiC or TiB Particles under Quasi-Static and High Strain-Rate Compression, Materials (2021) 14, 6837. DOI: https://doi.org/10.3390/ma14226837
Ballistic Test of the Multilayered Composite (Ti64+TiB) Armor Plate in this Project
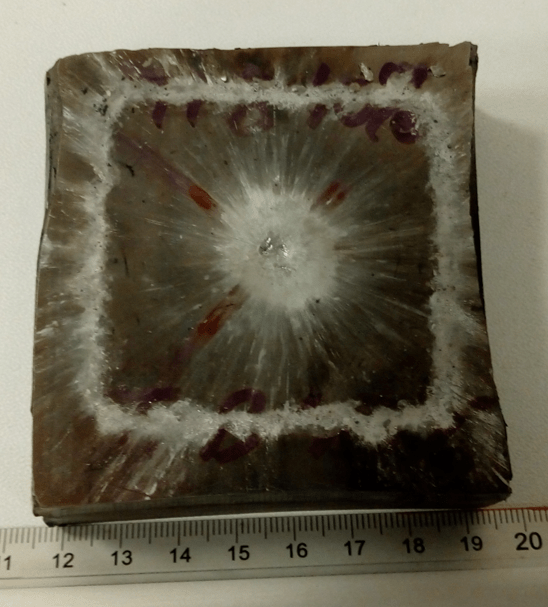
Figure 1: Results of shooting using the standard NATO bullet PP, caliber 7.62 (steel hardened core). Test was performed at Military Technical University, Warsaw, Poland (in collaboration with Prof. J. Janiszewski). The bullet was completely disintegrated and destroyed by combustion due to kinetic energy created during the impact (see video). The tested plate remained intact after examination, showing a small depression (about 2 mm deep) at the place of the impact in the armor plate.